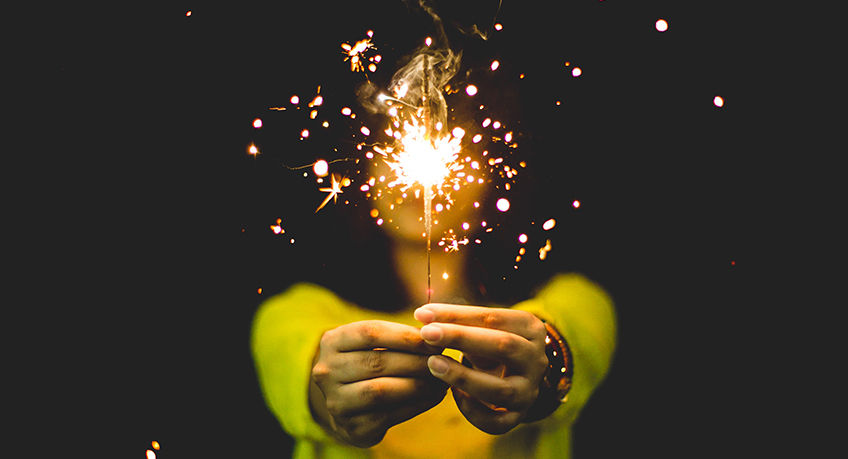
Energy costs for manufacturing facilities can be as high as 50% of OpEx (operating expenditure) so it is in the interest of all industrial companies to focus at least some of their efforts on energy management.
Reducing energy consumption in your manufacturing plant has two advantages: significant savings in operating costs plus a reduced energy footprint – being more environmentally responsible is a good thing.
Benchmark your current usage habits
Of course, the first step in reducing energy costs is to get clear on your current energy consumption, and which areas of the business are using the most, and at what time. Unfortunately, not enough manufacturing companies are able to gain these insights because they simply aren’t monitoring their energy usage.
Without real-time visibility of your varying energy needs, you cannot gain those significant insights which may translate into future operational changes for cost-saving.
Installing smart meters provides the necessary real-time monitoring across different processes within manufacturing units. They measure current, voltage, units (Kwh) and power factor and this data can be collated in an IoT Cloud Edge Gateway and published to the Cloud.
Limit the amount of data collected
A Cloud Edge Gateway can “do math” to process data at the Cloud’s Edge, this has several benefits:
Data can be processed in almost real-time so any action required is taken immediately rather than data making the round trip to the Cloud and back (this could be minutes or even hours) before action is taken.
Sensitive data can be kept within the existing network, maintaining the integrity of your company’s security without further investment or additional hardware and avoiding issues related to VPNs, DNS or firewalls.
Avoids a “data avalanche”. Stemming the flow of data and allowing only the vital and meaningful information to be carried to its final destination in the Cloud is more manageable and useful for human analysts.
Filtering data at the Cloud’s Edge reduces bandwidth and therefore bandwidth costs. Not a big issue when you have 5 devices but when you have 500 or 5,000, it all adds up.
The IoT platform can visualize this data into various charts and graphs to reveal peak demand, time-of-day spikes, seasonal trends, consumption patterns and other vital insights for each business unit/location.
This programmatic approach means old school manual entry/pen-and-paper recording of data can be abandoned and cast aside as the inefficient, time-consuming and large-margin-of-error activity that it is.
Uncovering potential savings tends to happen quite quickly after deployment as even basic information can be used to great benefit by the manufacturing company.
Getting started with your IoT energy monitoring trial
Begin with a pilot initiative monitoring one process or line, this way the required investment is kept low and the number of points of measurement is kept to a focused amount.
This will also assist you in getting buy-in from your manager. It’s likely this will be viewed as a pet-project for your department and a sandbox to keep you engaged.
For you it’s the chance to be seen as a pro-active employee interested in embracing new technologies and exploring new avenues for improvement and cost-saving in your department.
Be clear on what you’re monitoring and why. What are you trying to accomplish? Be as specific as you can with this as “cost savings” is woefully vague. How much, in what ways and by when? Define your KPIs in discussions with your wider team, and remember to start simple and small –complexity and scaling can come later.

How do you need to connect?
Everyone’s equipment is different. Some may already have sensors, and some may need “sensoring” first. What signals do you need to collate? TC, RTD, mA, V, mV, Potentiometer, Frequency, Pulse, Counter? Get those answers then consider the physical connections you require: RS232, RS485, WiFi, Ethernet, Cellular connection, or Bluetooth.
How many signals and from where?
A small number of signals and signal types means your energy monitoring initiative will likely be straightforward. However, if you wish to monitor multiple signals from multiple machines you may want to consider adding a gateway device to concentrate all the signals in one place.
Putting the data to use
After connecting your equipment and getting the data flowing, visualizing the information and putting it into a meaningful context will reveal insights and opportunities by studying your equipment’s/line’s current “energy consumption profile”.
Once enough data has been collected, you’ll get clarity on the energy usage fundamentals of your initiative and what types of changes are needed. Go for the small easy wins and perhaps one or two medium-term goals which may be more involved.
Expanding your trial
While conducting your energy monitoring trials it may be evident that you need to measure more than originally thought. Often these further requirements become obvious once you’re up and running rather than in the planning stage, this is new territory for everyone so don’t feel bad if something gets overlooked. Unless these additions prevent you from moving forward, save them for Phase 2 of your trial.
From monitoring to managing
Inevitably, successful energy monitoring trials grow and evolve into energy management policies for your business. Once trials conclude you can present the findings to your wider team and collectively draw some conclusions. Depending on the outcome this initiative may expand to further areas of the business, grow to monitor more machines or go deeper to conduct more sophisticated monitoring.
It’s likely that once you understand the variables which affect your power bill they’ll be an argument for automating and controlling these to make your facility more energy efficient and to optimize the energy that is used (doing more with less).
The checklist
Sensors
Energy meters
Edge Gateway (depending on number of signals)
Edge processing device (if not part of gateway features)
Cloud Service Provider
Data Visualization interface (dashboard)
Considerations
Try to keep your trial deployment as straightforward as possible and favor “Out-of-the-box” solutions over others which may require you to become an expert on every element in the chain from sensor to Cloud to dashboard.
Turnkey solutions are easier to pitch to management as they are provided by a singular vendor making procurement, deployment, troubleshooting and ongoing support far easier than dealing with multiple vendors.
Aim for simple installations with good connectivity and potential for scaling/expansion. Also pay attention to the ease-of-use of the software/dashboard, there are many that are powerful but fewer that are intuitive, graphically pleasing and user-centric.
Your choice of software is dependent on your choice of hardware so ensure they are compatible with each other.
An all-in-one vertically integrated solution
If you are attracted to a single solution which includes Edge Gateway, Cloud Service and web-based dashboard then Define’s Energy Monitoring solution should be on your list of possible options.
Straight forward set-up of the IoT gateway device, Define Cloud Services and data visualization dashboard means you can be up and running within minutes rather than months. The availability of APIs within the solution enables connection to internal business systems such as your ERP or CRM and external data sources such as Google maps, weather data or market spot pricing, making it even easier to take your first steps towards energy monitoring and management within your facility.